Rig-floor drilling robots improve quality control in repetitive tasks and eliminate people from red-zone exposure to dangers such as dropped objects and pinch points. Three robotic-drilling pilot programs were recently completed by TotalEnergies SE, Abu Dhabi National Oil Co. (ADNOC), and ExxonMobil Corp. TotalEnergies pilot tested four stationary all-electric drill-floor robots and ADNOC pilot tested hydraulically operated robots. Preliminary tests occurred at a dedicated facility, but pilot tests were also performed onshore and offshore. The robots successfully performed normal rig pipe-handling operations. The number of people in red zones was generally reduced by 50% and results from these studies showed that a high number of manual operations can be eliminated per year per rig, resulting in substantially safer operations.
XTO Energy, a subsidiary of ExxonMobil, deployed a fully automated land rig for its research and development drilling program in the Permian basin. The rig is still in the field.
Cloud-based robotic drilling
Robotic drilling allows digital devices to be used for monitoring and control. Digital drilling platforms integrate drilling apps and real-time drilling data with drilling plans (Fig. 1). Cloud-based systems send data to remote operation centers where data processing, including AI and machine learning, adjust drilling processes in real time to improve drilling metrics. Drilling progress is accessible to operators and subject matter experts worldwide through handheld apps.
Automated drilling systems monitor well trajectories to ensure they are within plan tolerances. Rotary dynamics, motor efficiencies, and directional drilling quality are available through on-demand slide sheet calculations. Rate of penetration (ROP), differential pressure (DP), and weight on bit (WOB) are constantly monitored through edge devices. Drilling disfunctions are automatically flagged when excessive fluctuations in ROP, DP, WOB, or torque are detected. Mechanical specific energy (MSE), a measure of formation drill-resistance close to the bit and a key lagged feature for ROP, is calculated in real time and drilling parameters adjusted to optimize ROP. “Machine-learning AI enhances Permian basin drilling,” detailed a digital drilling platform (OGJ, Jul. 5, 2021).
Hardware components for automated rigs are less developed. TotalEnergies investigated all-electric robots from Canrig Robotic Technologies AS while ADNOC studied hydraulically powered units from Frank’s International Inc. (part of Expro Energy Co.). XTO Energy deployed Nabors Industries PACE – R801 fully automated land rig in the Permian basin equipped with Canrig robotics in mid-2021, and it has been actively drilling since fourth-quarter 2021.
All-electric robots
TotalEnergies reviewed four stationary, all-electric, heavy-duty drilling and pipe handling robots with up to 7-ton capacity for dedicated tasks on the drill floor. These included a pipe sub handler, pipe handler, electric roughneck, and pipe deck handler (Fig. 2). These are among the largest all-electric robots in the world.
The test program included individual workshop tests for each component, full-scale tests of all four robots operating as a system, pilot testing of the pipe handler on a land rig, and offshore pilot testing of the drill-floor robot on a semi-submersible rig.
Drill-floor robot
The drill-floor robot reaches the well center and handles drilling subs and tools. It has a capacity of 1,600 kg and an accuracy of a few millimeters. An air-purge system protects the interior of the robot from harsh offshore environments and potentially combustible gasses. Tools and operations include a spinner-gripper (handling spinning subs and stabilizers), robotic safety clamp, stabbing guide, mud bucket, and dope and wash buckets.
The robot has undergone 8 years of testing in shop and pilot sites, including a recent 5-month test offshore on a semisubmersible rig in the North Sea. Tests were conducted outside time-critical drilling operations. The table lists handling operations for subs.
This robot was the only one of the four tested in an offshore environment, and it was subsequently disassembled to inspect for corrosion. No damage was observed, indicating the air purge was providing effective isolation of the components from drilling mud, sea spray, and humidity.
The pilot program revealed that the robot needed a smaller footprint. Onshore testing and training showed that collision control was required for the robot’s operating system to avoid collisions with third-party pipe handlers. The robot also needed further development to be operatable by standard crew members with only a few days of training. Specialists were onboard for the pilot and were too often relied upon when problems occurred.
During onshore tests in autonomous mode, the robot performed real-time decisions and simultaneously received data from other equipment, leading to data overflow. Software and hardware upgrades resolved this issue and the robot performed properly during the offshore tests.
Robotic pipe handler
The single-arm robotic pipe handler contains one manipulator arm holding two grippers with spinning capabilities to handle subs, drill pipe super-singles, bottom hole assemblies (BHA), and casing up to 3,500 kg.
The pipe handler picks pipe up off the ground, rotates to the vertical, and spins the pipe into the stick-up. The operation is performed quickly and hands-free. It improves cycle time because the elevator and iron roughneck can be positioned while the pipe handler is spinning pipe into the stick-up.
The handler was installed on a land rig and workshop tested for 250 hrs over 2 years without mechanical or vibrational problems. The rig subsequently went to the Permian basin in 2021 and drilled, tripped, and cased 50,000 ft of pipe during normal production drilling operations.
Pipe handler stand-alone operations gave tripping speeds of 1,096 m/hr, but overall tripping speed averaged 580 m/hr including waiting time for hoisting equipment and non-optimized handovers. The system ran an average of 14 casing joints/hr, which matched the initial target range.
The dual arm robotic pipe handler increases payload over the single arm version and handles triple or quadruple drill pipe with 7,000-kg capacity and up to 13 5/8-in. casing sizes. It was workshop tested for 2 years for racking triples, spinning triples into stick up, and handling super singles (14 m) from horizontal to vertical.
Tripping was successful on 182 runs, but a stabbing device was added to ensure that stabbing is performed correctly even with slightly bent pipe. Tests also included offline stand-building of drill pipe and casing without a mousehole. The lower robot picks the pipe up off the ground in the horizontal position, spins to vertical, and hands off to the upper robot arm. The lower arm then picks up a second pipe, rotates, and the two manipulators spin them together using a wrench on the pipe handler structure. No other equipment is needed to build stands.
Electric roughneck
The electric roughneck handles pipe up to 13 5/8 in. but does not contain a spinner because robot pipe handlers can spin the pipe. It applies accurate torque up to 250,000 Newton-meter over an even distribution and does not require casing tongs or a second casing crew. Electric motors in the roughneck generate torque-turn curves, and the spinners on the robot pipe handler usually leave less than 105° for roughneck make up, well within its 180° stroke. Between the workshop and test site, the roughneck performed a total of 9,200 make-up and break-out operations.
Robotic pipe-deck handler
The pipe-deck handler finishes fully automated handling from pipe deck to stick-up, replacing swing cranes, belt conveyors, elevators, and manual transport of pipe from pipe deck into the well center.
The handler picks up pipe—up to super singles—from the pipe deck and spins it into the well center. Operation for 10 months at the test site resulted in 300 trips in and out of well while handling drill pipe, casing, and BHAs up to 13 5/8 in.
Full-up tests
Testing of the integrated system in a 120-m pre-drilled well capable of handling triple stands occurred at a dedicated site. The site included an elevator for hoisting pipe, but no drilling equipment (top drive) was included in the test. The driller cabin was replaced with a PC-equipped office (with video screens) to operate the system. A total of 45 rig operations were performed, including:
Tripping in and tripping out with drill pipe and casing from set-back.
- Tripping in and tripping out with drill pipe and casing from pipe deck.
- Offline drill pipe and casing-stand building.
- Installing and removing subs in the drill string.
- Picking up and laying down pipe.
- Troubleshooting connection problems.
The system handled 5-in. and 5 7/8-in. drill pipe and 7-in. to 13 5/8-in. casing. Tripping speed was 1,078 m/hr (for triples from set-back, no retract of dolly) which was about twice typical conventional Gulf of Mexico tripping.
Hydraulic robots
ADNOC Onshore and Franks International set up a hydraulic catwalk, casing running tool, remotely operated completion tools, and zone management systems for drilling and completion operations on a conventional rig.
The hydraulic catwalk replaced conventional pick-up and lay-down machines to transfer tubulars between the pipe rack and rig floor. It consists of an extendable trough to conform to the length required at the well center, reducing both swing weight of the tubular being picked up from the trough and space for push-back from the tubular, minimizing footprint. An onboard programmable logic controller (PLC) operates simultaneous functions on the catwalk to precisely position it on the rig floor with minimal excess movement. It is operated remotely but has backup manual control. The catwalk had no contact with personnel, picking up casing strings from adjacent casing runs (Fig. 3).
The casing running tool (CRT) has hydraulically actuated single-joint elevators to run and make up casing, replacing power tongs, casing elevators, spiders, and dedicated hydraulic power units. It handles tubulars from 4.5 in. to 18 5/8 in. The combination of the CRT and hydraulic catwalk removed 50% of personnel from the rig floor including the stabber, two tong operators, and two floor men. A remotely operated stabber substituted for the CRT in completion operations with tubulars less than 4.5 in. Pilot completion trials ran 3.5 in. tubing with the remote stabber.
Other remote completion equipment included air-operated elevators, remotely operated tongs, and an automated completion tubing make up system. These provide hands-free methods of handling the completion string. The system has real-time remote access capability. Software controls the completion tubing make-up kit and evaluates the quality of the connections. Thread inspectors and joint-analyzer unit operators are no longer required and removing tong operators from the rig floor eliminates hand and finger injuries. All make ups during the pilot trial were within acceptable tolerances.
A zone management system (ZMS) managed collision risks between other equipment, rig structure, and workers. The remotely operated stabber ZMS prevented collisions between the top drive and stabber by continuously monitoring and communicating top-drive position to rig crew through visual and audible alarms.
After the pilots, the systems were run on five rigs for casing operations and two rigs for completion operations. The number of people in the red zone and subsequent HSE exposure were both reduced by 50%. A 20% increase in tubular running speeds was observed across the rigs using CRT with the hydraulic catwalk. Completion running speeds were about 5% slower than conventional systems but were deemed acceptable due to the HSE advantages.
XTO Energy fully automated rig
XTO Energy deployed Nabors Industries PACE – R801, the first fully automated land rig, in the Permian basin (Fig. 4) mid 2021. It combined Nabors’s Smart Suite of automated drilling software with Canrig robotics to remove crews from the red zone. A pipe-handler robotic arm and robot roughneck work together like the TotalEnergies pilot system to pick up and run pipe. Crew size on the rig is like other rigs but with altered duties. One driller supervises operations while others service, maintain, inspect, and move the rig.
The automated drilling software has a rig-operating system which monitors workflow for automated directional drilling. A drilling-plan tool provides step-by-step drilling instructions based on best practices, a drilling-activity sequencer steps through drilling processes, navigation software provides slide or rotate instructions on a stand-by-stand basis to defined steering tolerances, and an automated directional steering control system follows the planned wellpath with real-time visualization and analysis of planned vs. actual drilling trajectory. The system is accessible through a cloud-based platform using standard well information transfer specification (WITS/WITSML) protocols for remote operations and monitoring from any device.
The rig is contracted to drill three horizontal wells on a test pad in Midland County, Tex., for research and development. The first well reached total measured depth of 19,917 ft in October 2021. Detailed results from PACE – R801 are considered proprietary and have not been released.
Bibliography
Mwansa, P.L., Varma, E.N., Grayson, P., Norton, J., Webber, D., and Ligardo, E., “Enhancing Operational Safety Through Mechanization and Intelligent Automation of Drill Floor Operations,” SPE-207891-MS, Abu Dhabi International Petroleum Exhibition and Conference, Abu Dhabi, Nov. 15-18, 2021.
Raunholt, L., Meissner, S., and Kverneland, J.O.G., “Field Experience from Robot Tests on Drill Floor and Pipe Deck,” SPE-208010-MS, Abu Dhabi International Petroleum Exhibition and Conference, Abu Dhabi, Nov. 15-18, 2021.
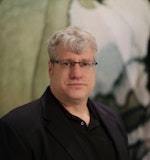
Alex Procyk | Upstream Editor
Alex Procyk is Upstream Editor at Oil & Gas Journal. He has also served as a principal technical professional at Halliburton and as a completion engineer at ConocoPhillips. He holds a BS in chemistry (1987) from Kent State University and a PhD in chemistry (1992) from Carnegie Mellon University. He is a member of the Society of Petroleum Engineers (SPE).