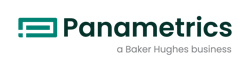
Flare stacks, those recognizable flaming pipes that poke out from oil refineries, LNG plants, offshore platforms, chemical and petrochemical plants perform an essential safety role task.
They are an essential safety device to safely dispose of gas if another part of the facility has to be shut down suddenly. It is often methane-heavy vent gas, and methane packs a potent punch as it’s estimated to have at least 25 times the warming potential of carbon dioxide over a 100-year period.
Operators and regulators recognize the importance of achieving high combustion efficiency (CE) of flare gas in order to reduce these methane emissions. When properly burnt off, the gas converts to carbon dioxide and prevents raw methane from entering the atmosphere via the flare stack.
“For many of our production sites outside of our onshore US business, flaring is the single largest source of methane,” says Peter Evans, the London-based environmental scientist from BP tasked with finding better ways to measure methane. “People worry about [gas] leaks but in reality leaks are often a small component when it comes to emissions. Enhancing the accuracy of measurements on flares offer far more potential for methane reduction.”
There’s a lot to measure: satellite data was used to estimate that 150 billion tons of gas was flared by the industry in 2020, the highest level since 2009.
There are other significant contributors to methane in the atmosphere, including agriculture and landfill. But, says Evans, “We in the oil and gas sector can address the methane emissions that come from our operations because they are focused and localized in ways that they may not be for other industries.”
BP’s ambition is to be a net-zero company by 2050 or sooner, and to support others to get there, too. This ambition is supported by 10 aims, including aim 4: “To install methane measurement at all our existing major oil and gas processing sites by 2023, publish the data, and then drive a 50% reduction in methane intensity of our operations”.
As part of that plan, BP is using flare.IQ to help better understand, measure and ultimately reduce methane emissions. It’s an advanced flare control and digital-verification platform developed by Panametrics, a Baker Hughes company, and part of the company’s broad emissions management capabilities. The flare.IQ solution sits on a plant’s control system, constantly measuring emissions and providing real-time data so that operators can ensure the flare is running at the targeted 98% CE.
The flare.IQ technology was originally developed to help oil and gas refineries meet EPA regulations in the US. “For example, the EPA requires you to monitor your flare every 15 minutes for it to be compliant,” explains Evans. “Technologies such as flare.IQ, service that part of the value chain, and those types of flares.”
About two years ago, Evans and his team started talking with Baker Hughes about BP’s ambitions around methane measurement and if flare.IQ could have value for upstream production facilities.
The two companies began working together and ran the first trials in 2020, a speedy deployment aided by some lateral thinking on the collaboration. At first, explains Evans, they were trying to work out how to make physical adaptations to the refinery control systems. “We were running into technical challenges as to how we’d upgrade the hardware to test this new software,” he says.
One of his BP colleagues pointed out that all the data they needed to run the computations was already being streamed into the cloud. Why couldn’t they just take that data, process it somewhere else and then stream it back to the facility? Says Evans, “using the power of cloud computing made it a far simpler deployment – on a lot of sites we may never have to visit to install flare.IQ. It’s a bit like downloading a new app on your phone – you don’t have to go to the phone store on the high street to do it.”
''Using the power of cloud computing made it a far simpler deployment.''
Peter Evans, BP
The power of flare.IQ is that it takes real-time measurements and instantly turns them into information, so that operators can quickly tweak their combustion process if they need to improve their CE.
“It’s a series of computational models that turn the raw data into an output that is functionally useful in terms of showing us methane intensity,” says Evans, who is a geoscientist with a PhD in geochemistry and an MBA in technology management. “It gives us real-time data on the performance of the flare, and we can see if it’s not hitting the standards that we need it to meet.”
The first trial site for flare.IQ was on a FPSO (floating production storage and offloading) facility, operating in the North Atlantic Ocean. For the inaugural six-day trial, BP used the vessel’s existing control system ‘’to take all the information from the flow meters, run the flare.IQ algorithms and provide that real-time feedback, ‘’ explains Evans.
The data showed consistently very high combustion performance standards, above 99%, consistent with the way it was designed. What flare.IQ gives BP, says Evans, is absolute verification of that. “There’s confidence for the operators on the vessel that as they get this feedback from flare.IQ, they can see how the flare is performing. And if there is a change in performance because a component needs maintenance, or environmental conditions are putting extra stresses on the flare, they can act and make any necessary interventions right there, right then.”
It was all delivered, says Evans, “through advanced analytics, without needing extensive changes to the way the flare is built or operated, and it hasn’t required a service engineer to go out and physically change anything on the system”.
The value of swift, low-touch deployment to BP’s sustainability targets is immense. “It means it’s something we can adopt rapidly, and that matters,” he says. “We have to bring our emissions down while maintaining operational productivity to keep global supplies of energy where they need to be. The ability to use data that’s already in our systems is an important message beyond this technique … there’s a lot of things we can do with that data at a level of sophistication that historically we may not have done.”
“It means it’s something we can adopt rapidly, and that matters”
Peter Evans, BP
As flare.IQ is rolled out to more BP facilities, Evans is excited about the potential. “The more you deploy, the more you learn,” he says. “There’s no such thing as too much data and the more we learn, the more we can understand the algorithms better, refine our systems and demonstrate the average efficiencies on a global basis of our flares as part of our reported values.”
Meanwhile, the capabilities of the flare.IQ platform are also growing. “In the latest release, we’re able to do remote verification of flare efficiency, which means no manpower, no infrastructure, no need to take the meters off,” says Diarmaid Mulholland, Vice President of Panametrics at Baker Hughes. It’s “enabling immediate action … to help those who operate flares take meaningful action fast. It’s a very exciting space, where we can bring real efficiencies that have a real impact on the environment. For example, if we take a facility operating at 70% flare efficiency, deploying flare.IQ will achieve 98%+ efficiency – the emissions savings is the equivalent of removing some 34,000 cars from our roads.”
Evans is rightly proud of BP’s efforts to reduce methane emissions and says that industry as a whole is running ahead of regulations.
“Normally regulations are created first, and then industry works to meet those regulations,” he says. “BP and other resources companies, trade associations and other bodies that have been created, all recognize how important it is to reduce methane emissions to help address climate change. We are making commitments to our stakeholders and shareholders that are informing the regulators, who are only now starting to embody it in law. The order in which these things play out has actually switched, and the industry is moving faster than the regulators are.”